Metal Die Casting for Strong,
Reliable Electronics Enclosures
Customer Benefits
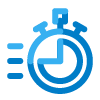
High Speed Production
Complex shapes within closer tolerances than many other mass production processes. Little or no machining is required and thousands of identical castings can be produced before additional tooling is required.
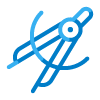
Dimensional Accuracy and Stability
Die casting produces parts that are durable and dimensionally stable while maintaining close tolerances. They are also heat resistant.
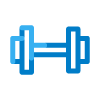
Strengh and Weight
Stronger than plastic injection moldings with the same dimensions. Thin wall castings are stronger and lighter than those possible with other casting methods.
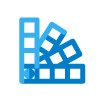
Multiple Finishings Techniques
Die-cast parts can be produced with smooth or textured surfaces, and they are easily plated or finished with a minimum of surface preparation.
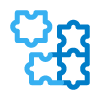
Simplified Assembly
Die castings provide integral fastening elements, such as bosses and studs. Holes can be cored and made to tap drill sizes, or external threads can be cast.
How are Die Castings Produced?
Clamping
Preparation and clamping of the two halves of the die.
Injection
The molten metal is next transferred into a chamber where it can be injected into the die.
Cooling
When the entire cavity is filled and the molten metal solidifies by cooling, the final shape of the casting is formed.
Ejection
Die halves can be
opened and an ejection mechanism can push the casting out of the die cavity.
Trimming
During cooling, the material in the channels of the die will solidify attached to the casting.
The Machines
Hot Chamber Machine
Used for alloys with low melting temperatures, such as zinc, tin, and lead. The temperatures required to melt other alloys would damage the pump in direct contact with the molten metal.
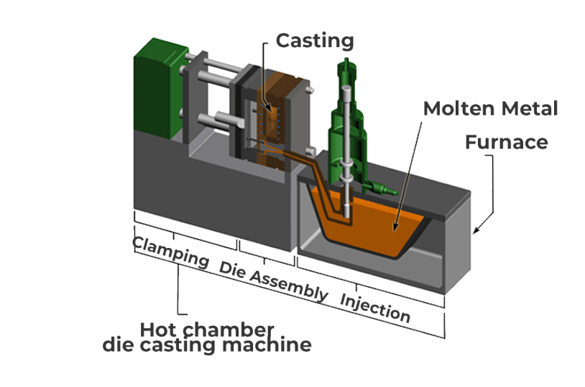
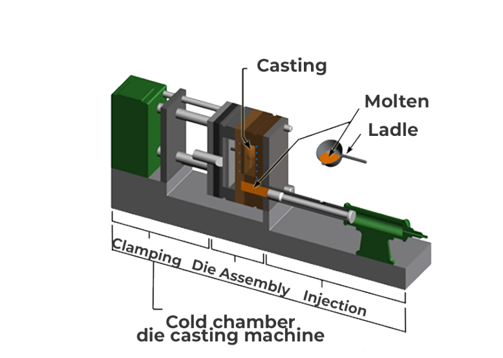
Cold Chamber Machine
Used for alloys with high melting temperatures that cannot be cast in hot chamber machines because they would damage the pumping system. Such alloys include aluminum, brass, and magnesium.
Cold chamber machine VS Hot chamber machine
COLD CHAMBER MACHINE | HOT CHAMBER MACHINE | |
---|---|---|
Materials Used | Alloys – Aluminum, Brass, Copper | Alloys – Zinc, Copper, Magnesium, Lead |
Temperature | Materials with high melting points | Materials with low melting points |
Chamber | Cylindrical Sleeve-Automatic-Hand Ladle | Gooseneck |
Closing System | Hydraulically Operated Plunger | Plunger |
Process | Cyclical | Ongoing |
Pre Treatments
Shot blasting
Technique is carried out by imparting the part surface using certain abrasive materials for preparing its surface. Used for surface preparation before the part is subjected to other operations like anodizing, painting, etc. Shot blasting can considerably improve the durability and longevity of the part.
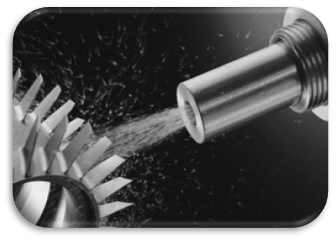
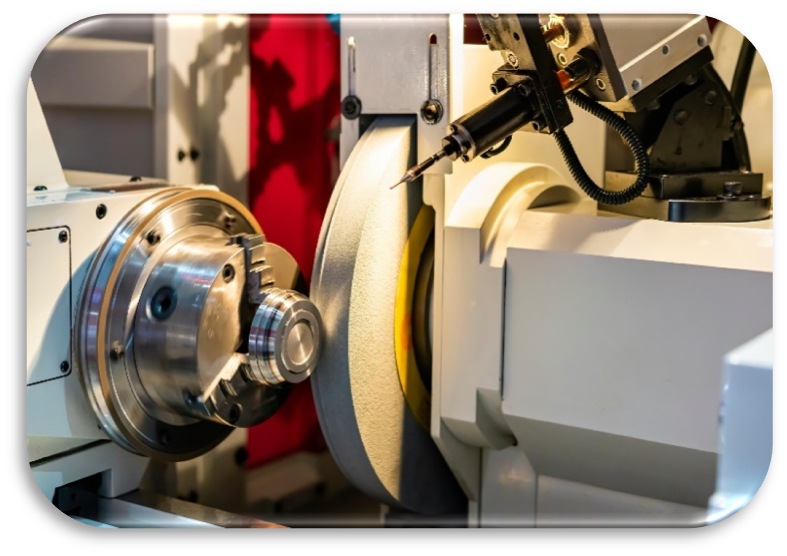
Grinding
To deliver a die cast part with nice smooth surfaces, without dividing lines or other defects, ready for surface finishes. Grinding.
Post treatments
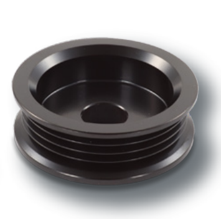
Black Hard Anodizing
The only available anodizing method for aluminum die casting parts. The corrosion resistance of the surface is greatly improved. This finish is highly recommended for the casting of outdoor applications.
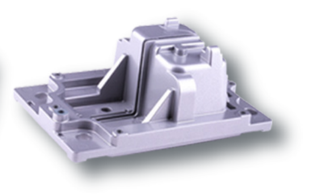
Powder Coating
Used not just as a surface decorative, but also to improve the surface corrosion resistance of the casting products. This process shields even the toughest and roughest machinery from corrosion.
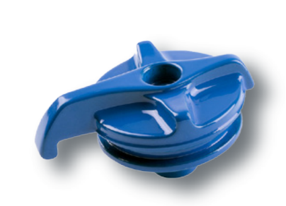
Painting & Stoving Varnish
Painting is usually used for surface prevention and decoration, whereas stoving varnish is comparatively an expensive process and it is mainly used for decorative die casting parts.
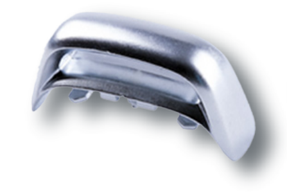
Mirror Polishing
Brushing is used for the decoration of die cast products. Polishing is actually a necessary process that needs to be performed before any other surface treatment methods including stoving varnish, electroplating, or powder coating.
Applications
Any questions?
There is an ICAPE Group team close to you and your business. All around the world, our business units are staffed with native experts available to answer all your questions. Contact us today!