CAF: Understanding Conductive Anodic Filament on PCBs
Let’s explore a fascinating undesirable aspect of PCBs called Conductive Anodic Filament (CAF). CAF is the growth of electro-migration copper between two conductors. In this article, we’ll talk about how PCBs are made, what causes CAF, especially Multi layers with increased design density, and possible measures to prevent or limit the risk of CAF.
What is CAF?
Conductive anodic filament failure is the growth of electro-migration copper between two points in a printed circuit board.
The CAF failure reduces the resistance and finally creates a shortcut between two oppositely biased copper conductors.
CAF failure can occur between conductors as: plated hole to plated hole, plated hole to trace, or trace to trace. The most common failure modes are between plated holes & between plated holes to traces.
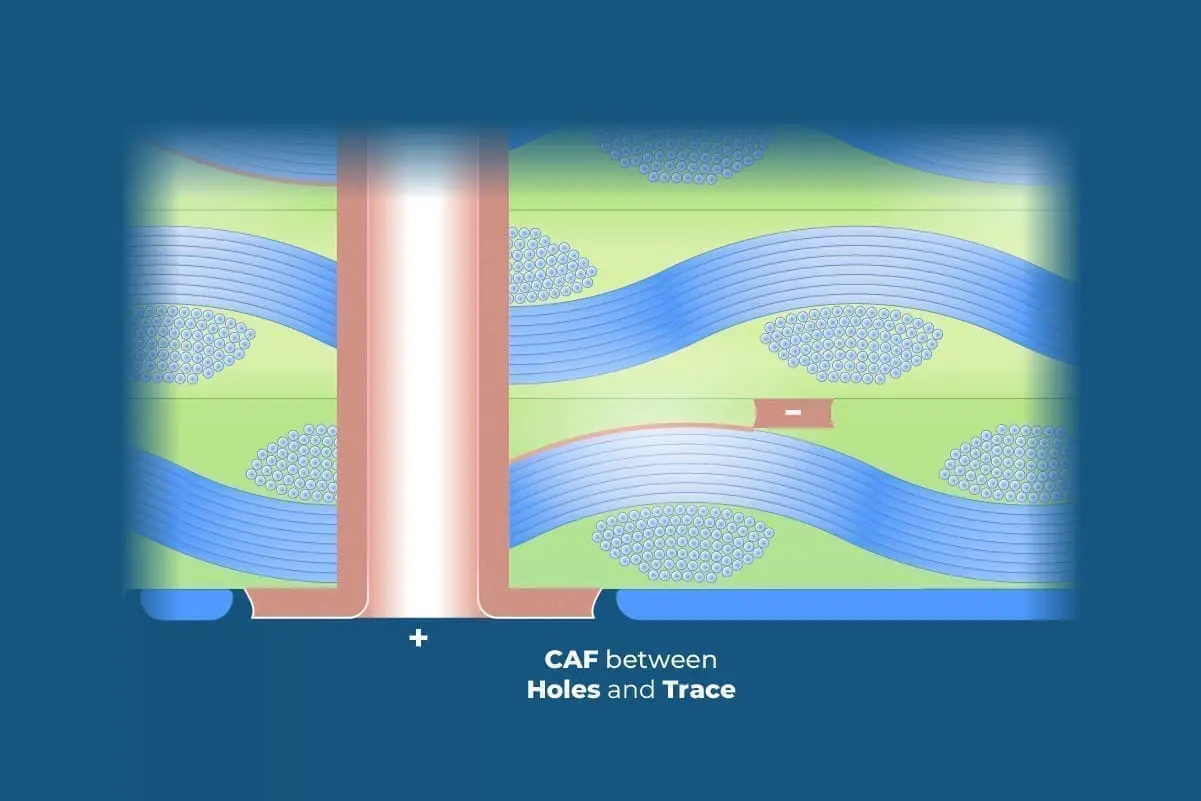
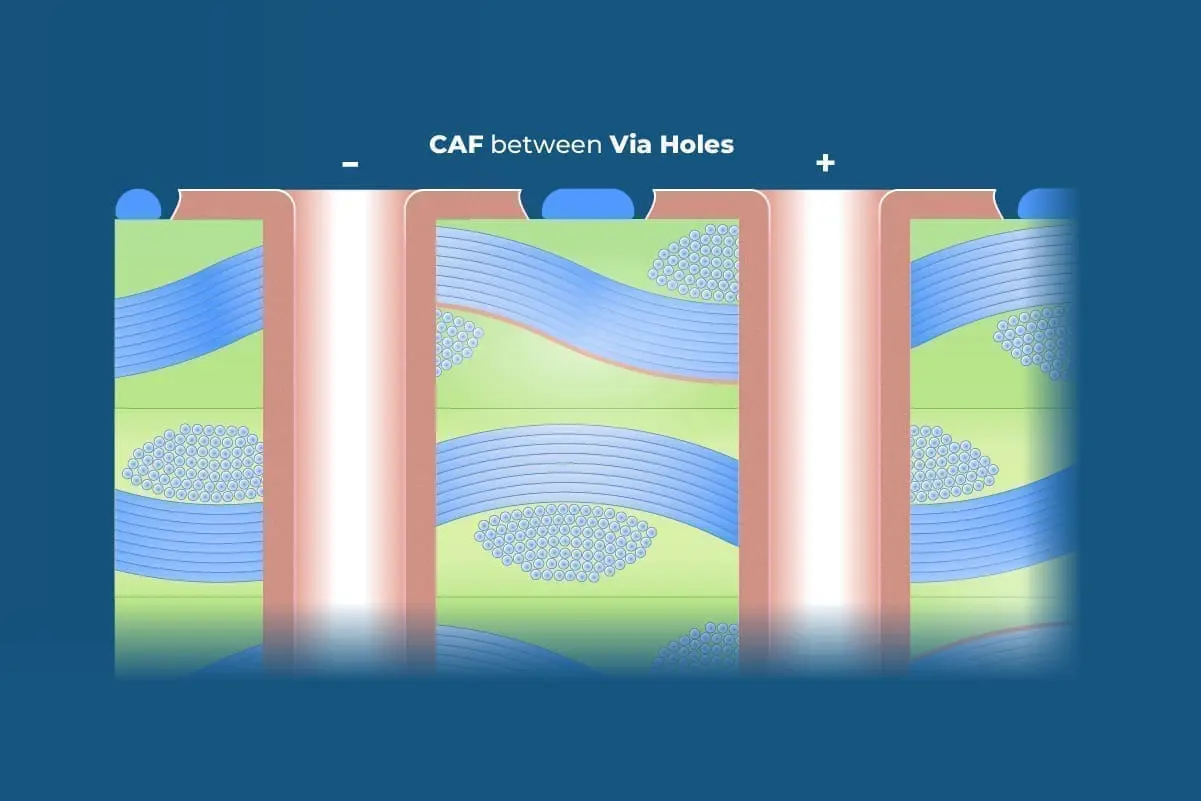
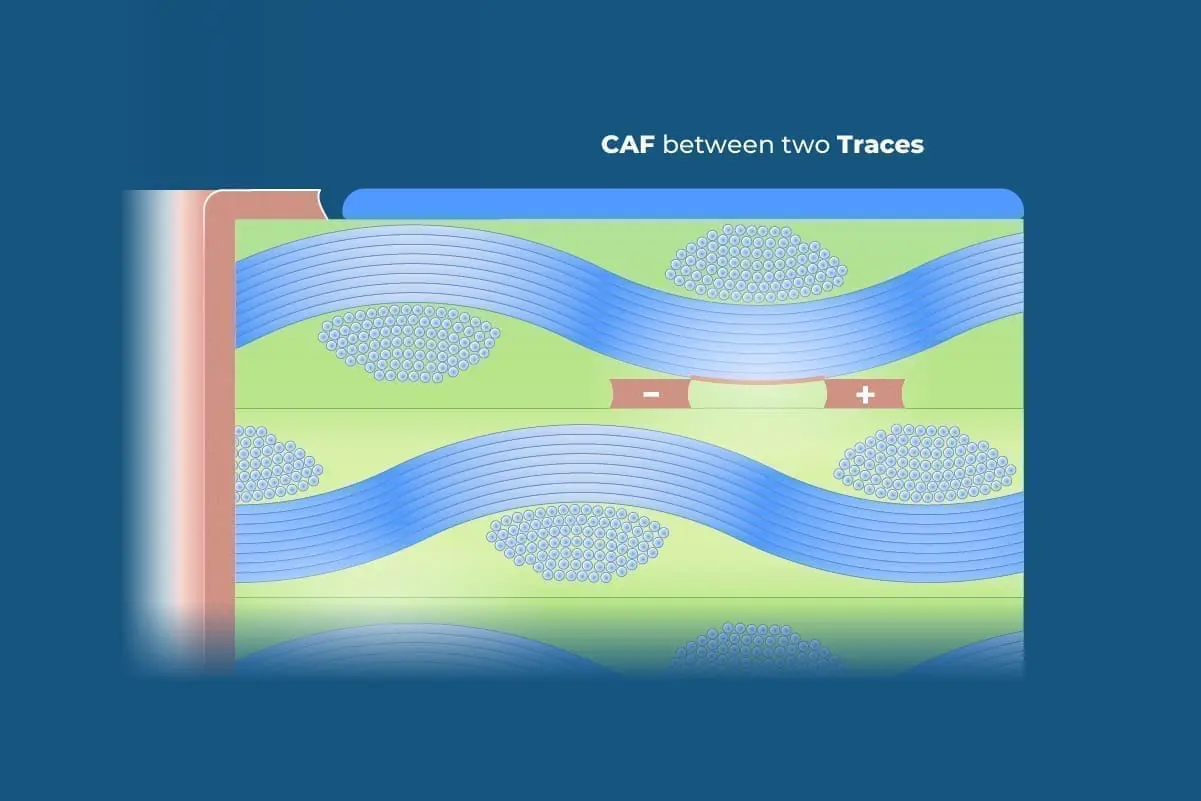
The CAF failure has two stages:
Stage 1
The degradation of the interface between the resin and the woven glass
The known main factors influencing the first stage are the humidity and temperature conditions in the PCB.
Baking/drying the PCB seems to have a reversable effect on the first stage. It amplifies the importance of keeping the PCB in dry conditions during the PCBA process as well in the applications lifetime.
Stage 2
The growth of electro-migration copper between the conductors
This stage can begin after the degradation of the resin/glass interface. The known main factors influencing the second stage are distance between two opposite biased copper conductors, placement/angle between holes versus glass fiber direction, voltage bias, humidity, temperature, and pH concentration.
“The conditions for cu ions to migrate from the + charged conductor to the – charged conductor along the interface between the resin and the glass fibers can be compared to the conditions of a galvanic Cu plating process. The copper migration formation is irreversible and the formation is unaffected by baking/drying when CAF has completed.”
Understanding PCB Manufacturing Process
To have a better understanding of CAF, let’s review how PCBs are made. In multilayer constructions, plated holes create connections between the individual layers in the stack-up. After the hole drilling and hole cleaning a thin layer of chemical Copper or similar conductive material is applied to the PCB surface and holes before the final galvanic Copper plating.
Preventing CAF
Material Choice: Reduce the risk of CAF by specifying high Tg. and CAF resistant material.
Design: Delete non-connected pads on inner layers but keep the isolation distance as if there were pads on the inner layer. This will reduce the risk of CAF by increasing Cu to Cu distance. Avoid voltage vias next to ground vias whenever possible. When it is unavoidable then do not place the vias aligned with the woven glass. Displace them in angle of 45°, to prevent formation of CAF along the glass fibers. Furthermore, it is recommended to increase the spacing between such vias.
PCB Manufacturing: The manufacturer shall focus to limit/avoid voids during the lamination process. The drill parameters feed/speed must be balanced to prevent any early stages degradation of the resin/glass interface. The hole de-smear chemistry shall be firmly removed before the Cu plating to prevent any acid contraption between the FR4 and the Cu plated hole wall.
PCBA Assembly: Make sure that the PCBs are in a dry condition before the solder process. Trapped moisture inside the PCB can during the soldering turn to steam and cause micro delamination, which over time can lead to CAF.
Cleaning after Assembly: Thoroughly clean the PCB after assembly to remove any contaminants that could cause CAF.
Protective Coating of the PCBA: Apply a protective coating to the PCBA to shield it from moisture, salt, and other damaging substances during the applications lifespan.
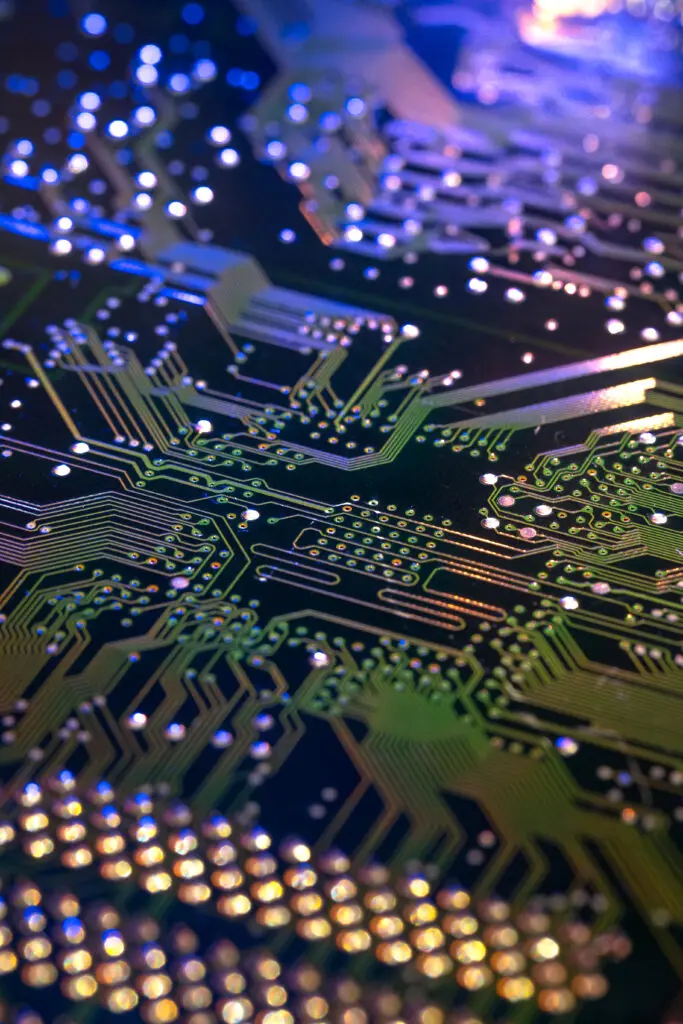
Conclusion
CAF can occur on all FR4 based PCB types but as mentioned above certain conditions accelerate the phenomenon which leaves some applications more vulnerable to CAF than others. High current PCBs and PCBs with a high wiring density seem to be the most affected, especially if they are exposed to high operating temperature and humidity.
However, knowing the conditions are the first step to prevent CAF by:
- using CAF resistant material
- design with focus on spacing and placement of GND and VCC vias
- choosing supplier with good process control
- ensure dry conditions before soldering
- clean PCBs after assembly
- use protective coating to shield PCBAs operating in harsh environments
If you need more information, contact us at ICAPE Group.
Author : Erik Pedersen/Jordan Labbe
Our latest news
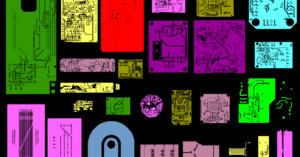
PCB Pooling Techniques : Benefits & Limitations
PCB Pooling Techniques Benefits & Limitations What Is PCB Pooling? PCB pooling is a special manufacturing technique where different customers’ PCB circuit designs are combined
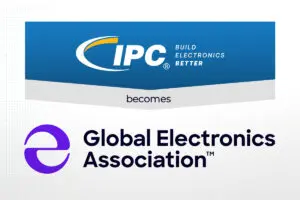
IPC Becomes the Global Electronics Association
IPC Becomes the Global Electronics Association (GEA) The electronics industry is entering a new chapter as IPC officially rebrands itself as the Global Electronics Association
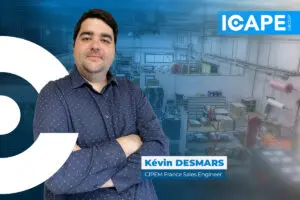
Integrating a new type of conductive ink
Integrating a new type of conductive ink Kevin Desmars : From the Lab to the Factory! Kevin Desmars has always had one foot in fundamental
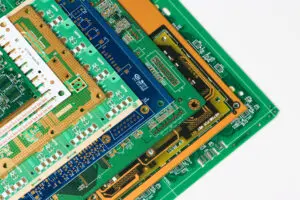
PCB Technologies: The Ultimate Guide – Applications, Advantages, and Industry Insights
Guide to PCB Technologies Applications, Advantages, and Industry Insights Printed Circuit Boards (PCBs) are the essential foundation of nearly every electronic device—from smartphones and medical
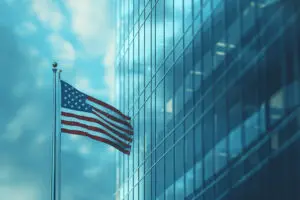
Monitor U.S. Import Tariffs on PCBs & Technical Parts
United States tariff information In April 2025, the United States has implemented new tariffs on Chinese imports, including printed circuit boards (PCBs) and custom-made technical
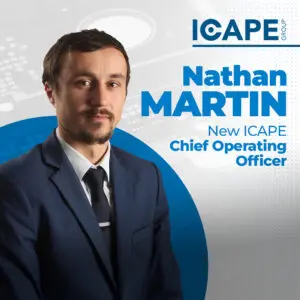
ICAPE Group Appoints Nathan Martin as Chief Operating Officer
ICAPE Group appoints Nathan Martin as Chief Operating Officer ICAPE Group announces the promotion of Nathan Martin to the role of Chief Operating Officer (COO).