Introdução às microvias PCB HDI
Desvendando as maravilhas em miniatura
As placas de circuitos impressos (PCB) têm sido a espinha dorsal dos dispositivos eletrônicos modernos durante décadas. À medida que a tecnologia avança, aumenta a procura por dispositivos menores, mais leves e mais eficientes. As microvias PCB desempenham um papel crucial na satisfação destas exigências. Este guia abrangente explorará o mundo das microvias PCB, seus tipos, processos de fabricação, aplicações e considerações essenciais do projeto. Quer seja um designer de PCB experiente ou um entusiasta curioso, este artigo desvendará as maravilhas em miniatura que alimentam a eletrônica do futuro.
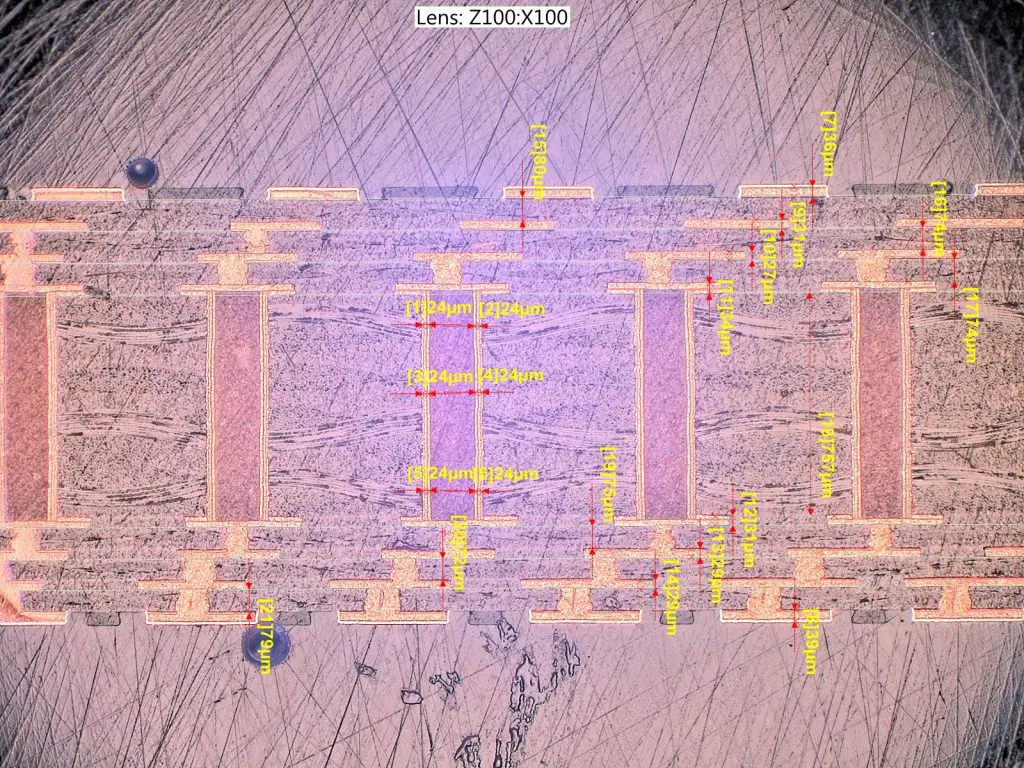
O que são Microvias PCB?
As microvias são pequenos orifícios que atravessam uma ou mais camadas de uma placa de circuito impresso, normalmente com diâmetros que variam entre 0,1 mm e 0,15 mm. Estas maravilhas microscópicas atuam como vias para sinais ou ligações de energia entre diferentes camadas da placa, permitindo interligações de alta densidade.
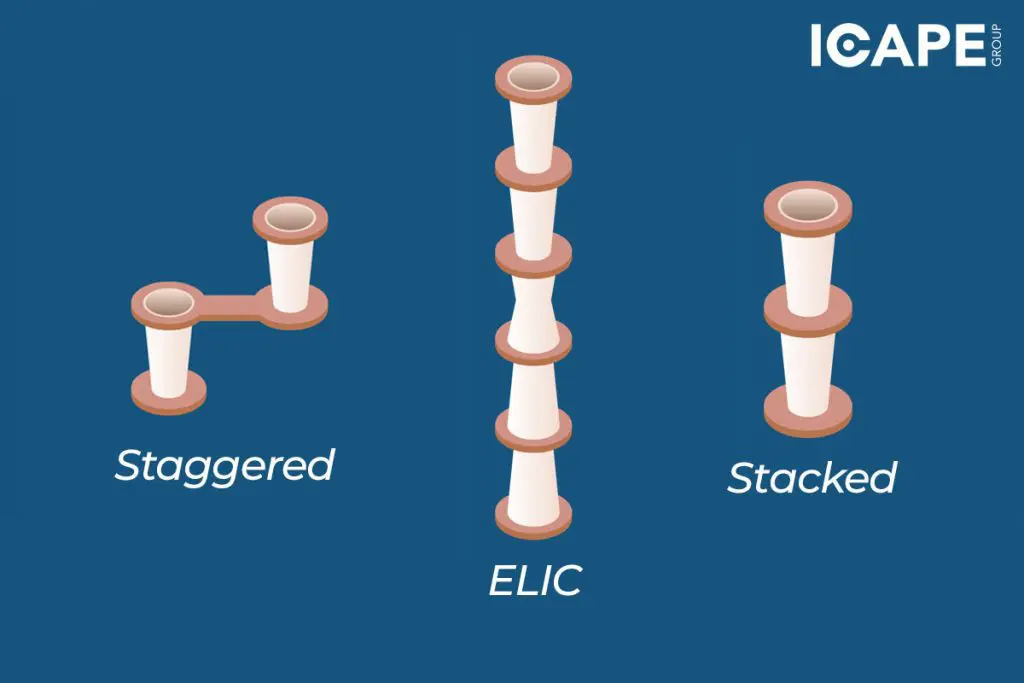
O que são Vias e Microvias?
Os orifícios de vias são usados para criar uma interligação elétrica ou térmica entre camadas de uma placa de circuito impresso. Há basicamente 4 tipos de orifícios de vias:
- Through via holes – orifícios perfurados mecanicamente que atravessam todas as camadas do empilhamento.
- Buried via holes – orifícios perfurados mecanicamente que interligam 2 ou mais camadas internas.
- Blind via holes – orifícios perfurados mecanicamente que interligam a camada externa com uma ou mais camadas internas.
- Microvias – orifícios perfurados a laser que interligam uma camada com a camada seguinte no empilhamento. (É principalmente possível perfurar microvias mecanicamente, mas é muito mais fácil e econômico fazê-lo com laser.) O tamanho mais comum das microvias é de 80-100µm com uma profundidade de 60-100µm. A relação de aspecto é a relação entre o dielétrico que isola as camadas de cobre e o diâmetro do orifício. A maioria dos fornecedores exige uma relação de aspecto de 0,6: 1 a 1: 1 e o mais comum é 0,8: 1 (e. Dielétrico 80um Diâmetro de perfuração a laser 0,1mm). A nova geração de máquinas de perfuração a laser pode perfurar vias com diâmetros até 40-50um e algumas delas são mesmo capazes de fazer orifícios simultaneamente de ambos os lados de um material, o que cria a oportunidade de perfurar a laser dielétricos finos antes do processo de laminação. Isto é especialmente útil durante a produção de substratos IC como PCB.
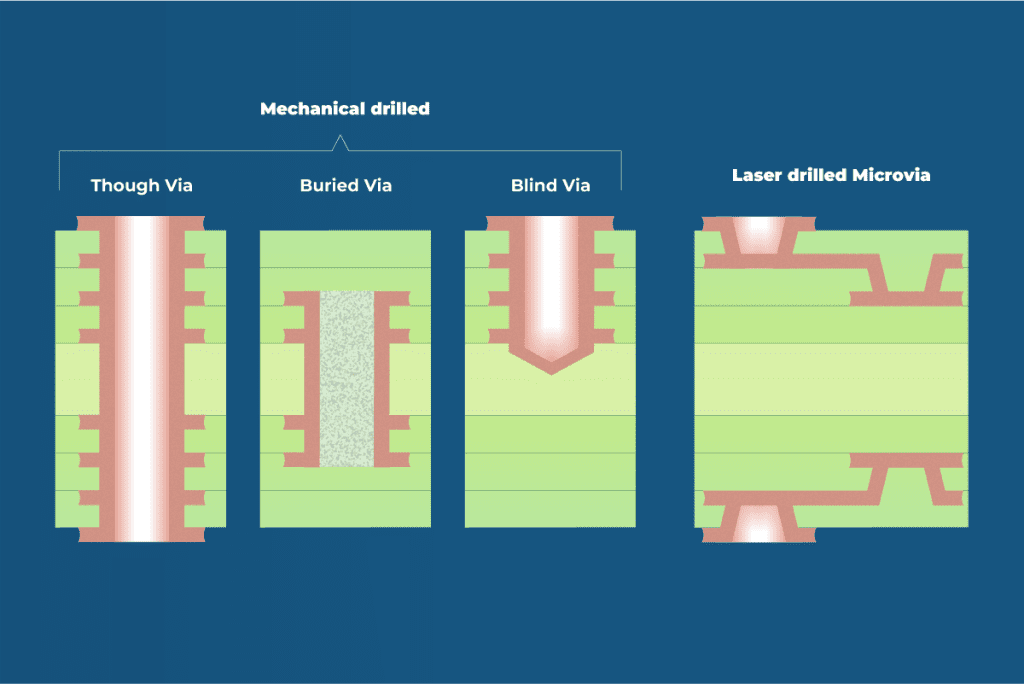
Estruturas de empilhamento HDI e etapas HDI
As PCB padrão com PTH (Plated Through Holes) requerem apenas 1 laminação, 1 perfuração mecânica, 1 limpeza de orifício, 1 revestimento químico de cobre e 1 revestimento galvânico de cobre. As estruturas HDI podem exigir que estes passos sejam repetidos várias vezes.
Todas as PCB HDI começam com a construção das estruturas da camada interna intermediária e repetem os passos de laminação, perfuração, limpeza e revestimento até à conclusão do empilhamento final. Vamos mostrar alguns exemplos abaixo.
A construção IPC-2226 tipo 1 requer apenas 1 laminação, 1 perfuração mecânica, perfuração a laser de um ou ambos os lados, 1 limpeza de orifício, 1 revestimento químico de cobre e 1 revestimento galvânico de cobre. Isto também é referido como HDI de 1 etapa.
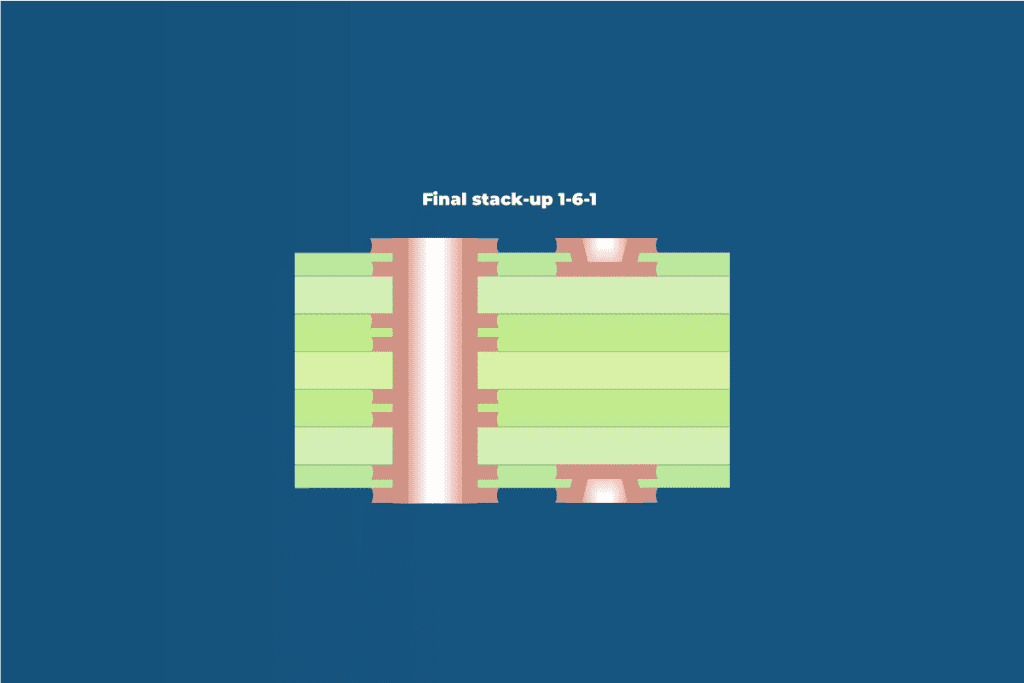
Quando a HDI de 1 etapa não é suficiente para suportar o passo dos componentes ou a densidade geral da placa de circuito impresso, podem ser acrescentadas vias enterradas adicionais para aumentar a densidade da fiação. A construção IPC-2226 tipo 2 requer 2 laminações, 2 perfurações mecânicas, perfuração a laser de um ou ambos os lados, 2 limpezas de orifício, 2 revestimentos químicos de cobre, 2 revestimentos galvânicos de cobre e 1 enchimento de resina. Isto também é referido como HDI de 2 etapas.
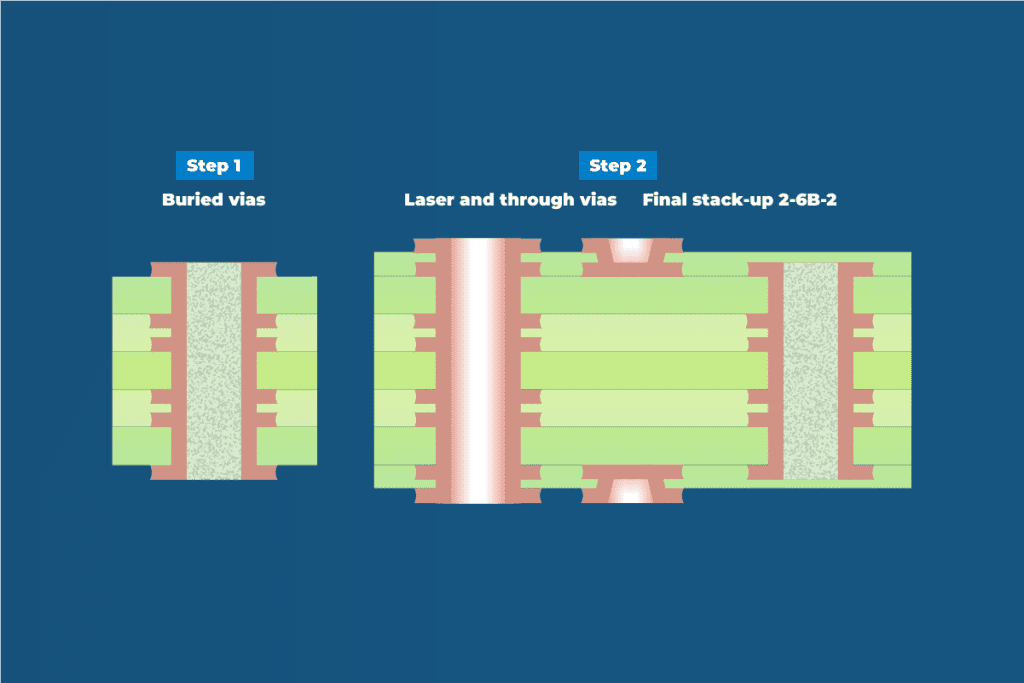
Quando a estrutura de tipo 2 não é suficiente para suportar o passo dos componentes ou a densidade geral da placa de circuito impresso, podem ser aplicadas vias a Laser e vias enterradas adicionais. As estruturas de tipo 3 contêm um mínimo de microvias de 2 etapas. A construção IPC-2226 tipo 3 mostrada abaixo requer um mínimo de 3 laminações, 2 perfurações mecânicas, 4 perfurações a laser, 3 limpezas de orifício, 3 revestimentos químicos de cobre, 3 revestimentos galvânicos de cobre e revestimentos e 1 enchimento de resina. Isto também é referido como HDI de 3 etapas.
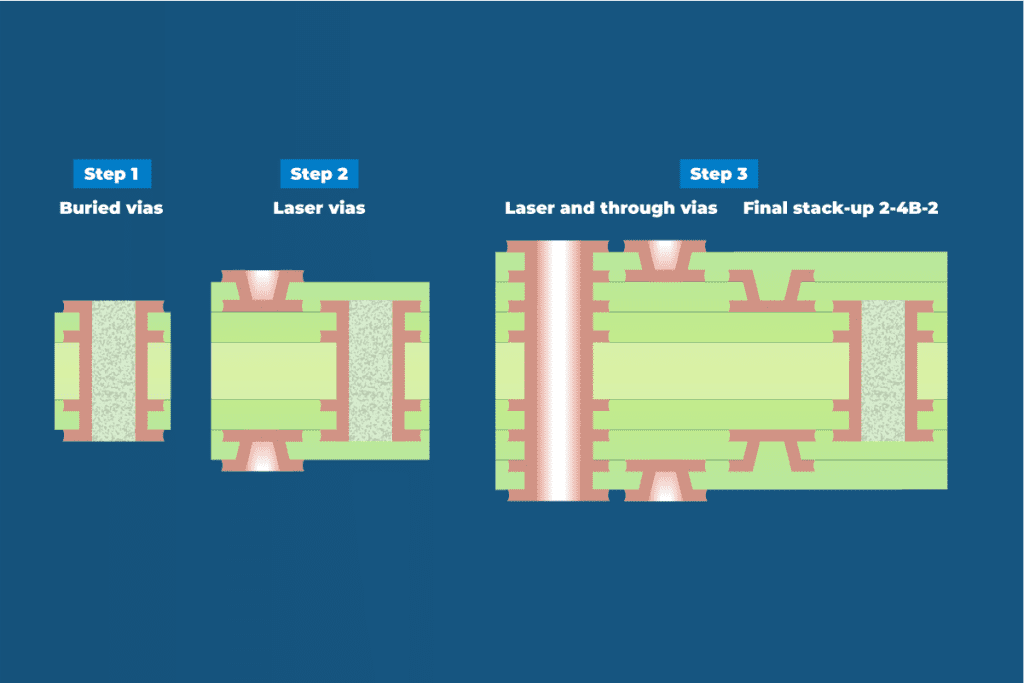
Desenvolvimento das etapas de HDI
O passo BGA evoluiu de 1,2 mm, nos primeiros componentes BGA, para 1,0 e 0,8 mm, em que as multicamadas que continham apenas a tecnologia through hole via eram suficientes para criar a interligação e os fan-outs eram possíveis com um design “dogbone”. Atualmente, a maioria dos componentes BGA só está disponível com um passo de 0,5 mm ou inferior, o que significa que a tecnologia HDI com vias perfuradas a laser é uma necessidade para fazer o fan-out. Na indústria dos celulares, começaram mesmo a ser usados componentes BGA com um passo de 0,2 mm.
Este desenvolvimento ultrapassa os limites da capacidade de produção e do equipamento usado para produzir PCB HDI.
Os designs de HDI mais complexos que contêm BGA com passo de 0,4-0,5 mm podem ser encaminhados com um máximo de 2-4 etapas de microvias de cada lado da PCB, mas alguns fornecedores dominam 5, 6 ou mais passos de microvias e o desenvolvimento da miniaturização de componentes continua ultrapassando os limites, indo na direção de ELIC (Every Layer Interconnection), também referida como Any Layer HDI, em que as vias empilhadas são implantadas através de qualquer camada do empilhamento.
Microvias empilhadas ou escalonadas / vias enterradas
O passo do componente do BGA, juntamente com o tamanho do bloco ou a densidade do design, ditará quando usar microvias empilhadas ou escalonadas / vias enterradas ou quando usar vias enchidas com cobre. Cada processo adicional aumenta o custo global da PCB. O encaminhamento firme dos fios e a seleção da melhor combinação de empilhamento HDI e vias podem contribuir frequentemente para a redução dos custos. O ICAPE gostaria de apoiar sua visão tecnológica com fatos e conselhos:
É importante escolher as combinações de vias e de passos mais adequadas para otimizar os custos da sua PCB.
O custo adicional de agregar um nível de microvia a uma estrutura 1-6B-1, criando uma estrutura 2-4(6B)-2 como a que se segue, é consideravelmente inferior ao custo de uma estrutura 2-4B-2. Tanto 1-6B-1 como 2-4(6B)-2 são construções HDI em 2 etapas, mas 2-4B-2 é um HDI em 3 etapas.
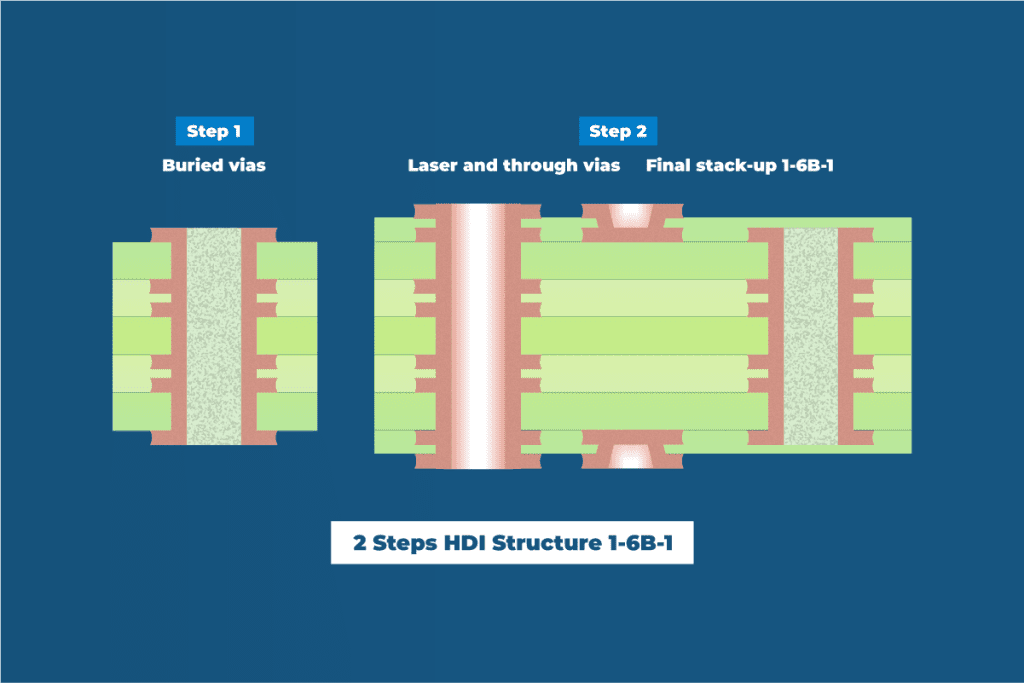
O único processo adicional que se agrega ao passar de 1-6B-1 para 2-4(6B)-2 é a perfuração a laser 2 vezes.
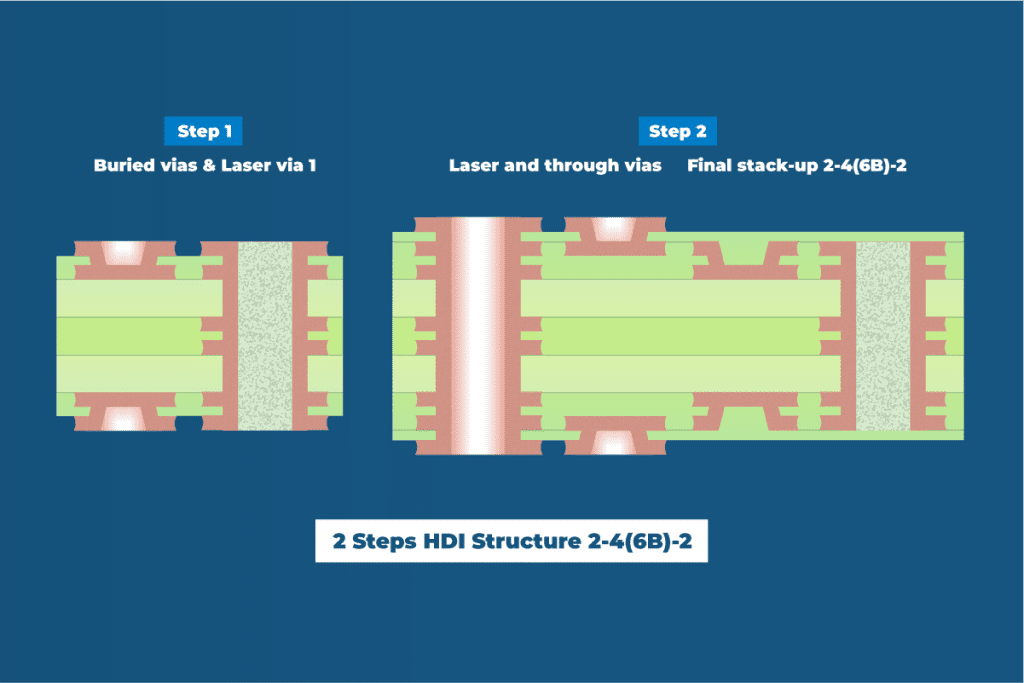
Passar de 1-6B-1 para 2-4B-2 requer uma etapa extra de HDI com perfuração a laser adicional de 2 vezes, 1 laminação extra, 1 limpeza de orifício extra, 1 revestimento químico extra e 1 revestimento galvânico extra.
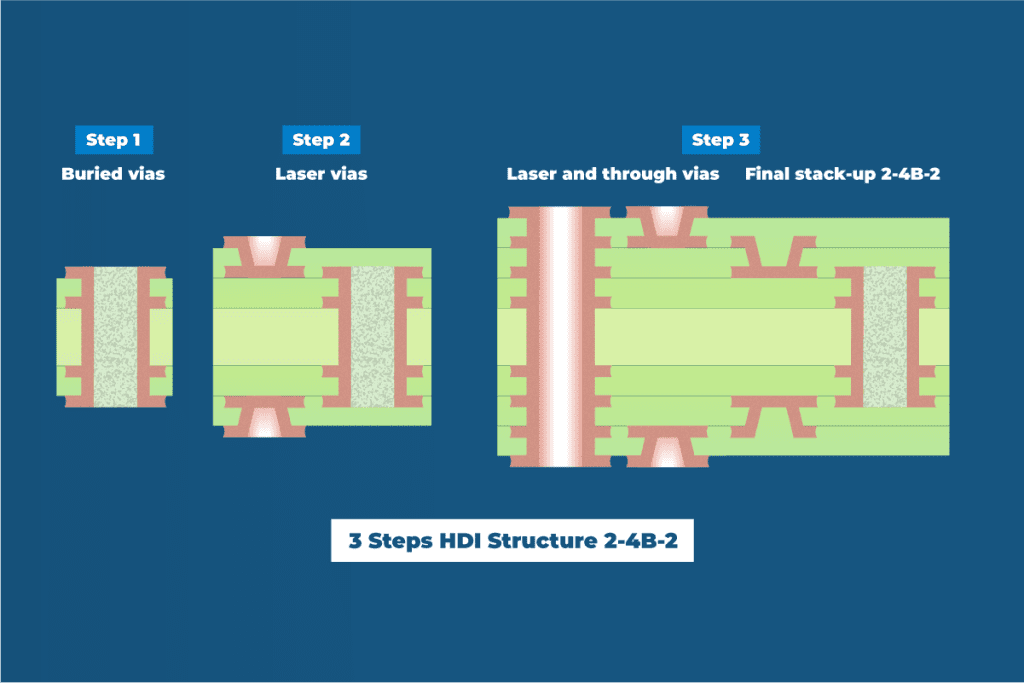
Vias empilhadas ou escalonadas?
As microvias empilhadas criam mais espaço para a fiação de alta densidade e para o fan-out dos BGA de baixo passo, mas aumentam o custo da PCB. As microvias empilhadas só devem ser usadas quando o design não tem espaço suficiente para usar vias escalonadas. As microvias empilhadas em vias enterradas requerem um processo adicional de revestimento de cobre para as vias enterradas e as microvias empilhadas em microvias requerem um enchimento adicional de cobre das microvias da camada interna.
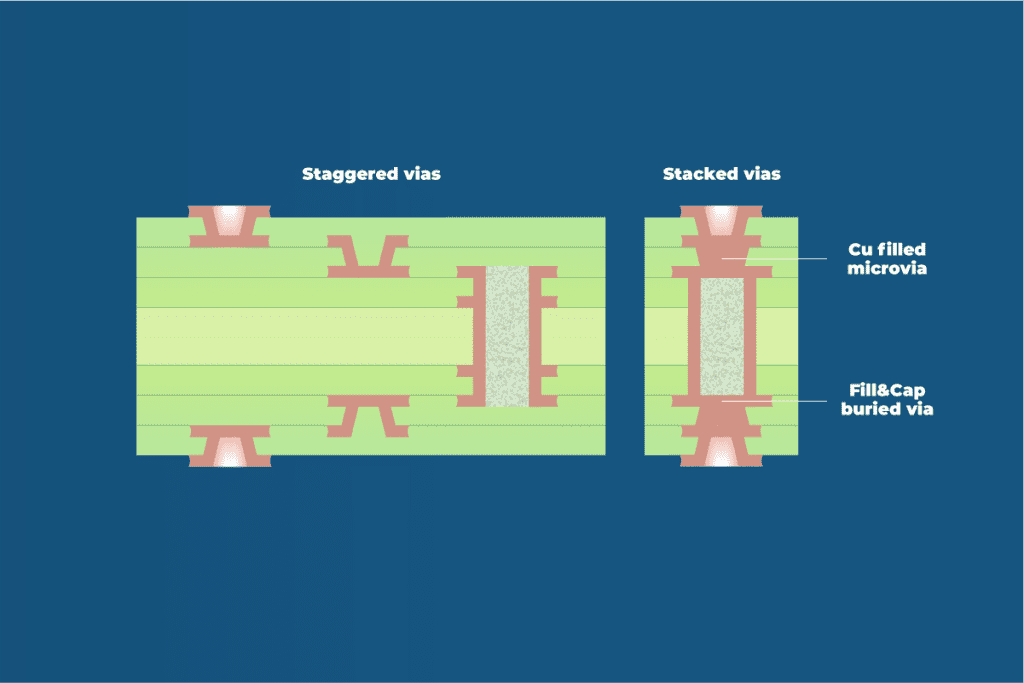
Microvias enchidas com cobre?
Os designs com microvias em bloco BGA ou em pequenos blocos de soldagem semelhantes podem beneficiar do enchimento de cobre, uma vez que este elimina a possibilidade de bolsas de ar nas juntas de soldadura, mas o enchimento de cobre aumenta o custo da PCB. Os designs sem microvias no bloco não necessitam de enchimento de cobre.
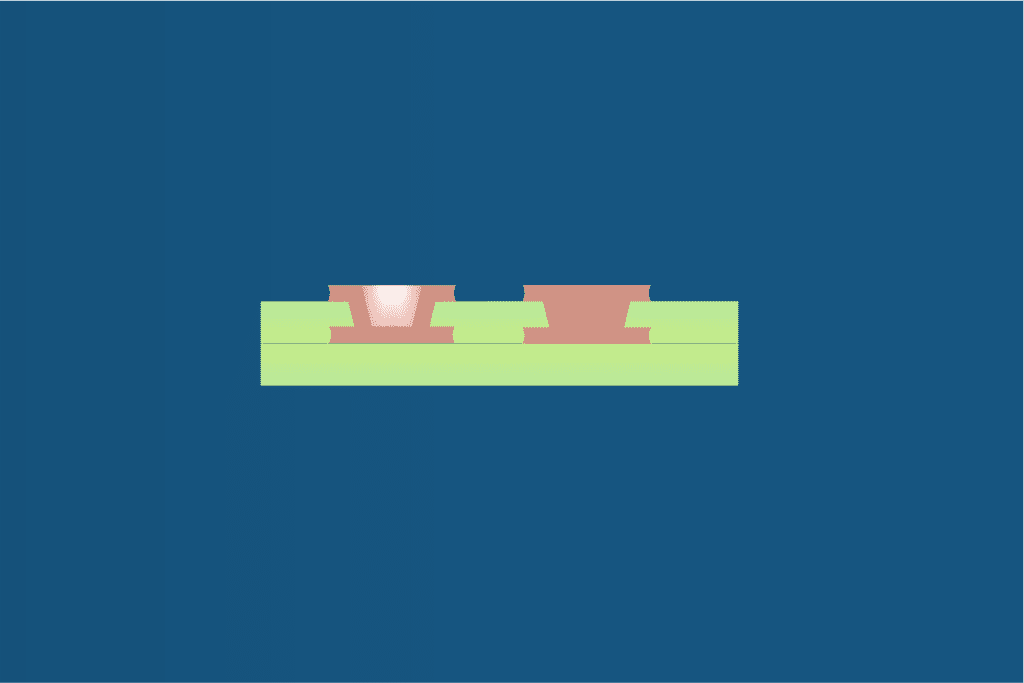
Integração da microvia no design completo
Quando é necessário usar a tecnologia HDI com microvias perfuradas a laser e vias enterradas devido à densidade da fiação ou ao fan-out do componente, faz todo o sentido substituir todas as vias perfuradas mecanicamente por microvias perfuradas a laser e vias enterradas, uma vez que isso reduzirá o custo de fabricação e o tempo de produção.
O processo de perfuração a laser é um processo muito mais rápido e mais barato do que a perfuração mecânica, comparando o custo de cada orifício. O preço mais alto de uma PCB HDI em comparação com as multicamadas padrão está relacionado com os processos adicionais necessários para cada etapa HDI. O custo da etapa do processo HDI é o mesmo, quer se usem apenas algumas microvias para o fan-out da fiação BGA, quer se substituam todas as through vias por microvias e vias enterradas. Neste caso, a substituição de todas as through vias reduzirá o tempo e o custo do processo de perfuração mecânica.
A substituição de todas as through vias em toda a PCB faz sentido:
– Criará espaço para uma fiação melhor e mais apertada, levando a uma maior população de componentes em menos espaço e com menor peso.
– Contribui para melhorar a integridade do sinal, controlar a impedância e reduzir as interferências eletromagnéticas, através de percursos de sinal mais curtos, linhas de transmissão reduzidas e melhor funcionalidade do plano de referência GND e VCC com menor penetração de orifícios.
– Elimina a necessidade de perfuração posterior nas through vias para evitar reflexos de sinal paralelos.
– As PCB HDI sem through vias são mais resistentes ao estresse térmico criado pelas altas temperaturas dos processos de soldagem.
Como são produzidas as vias de perfuração mecânica e as vias de perfuração a laser?
Ver Percurso de Fabrico de PCB ICAPE episódio 5 Perfuração.
As microvias laser HDI revolucionaram a indústria eletrônica, tornando possível colocar mais funcionalidades em dispositivos mais pequenos e mais leves. À medida que a tecnologia continua evoluindo, as microvias permanecerão na vanguarda da inovação do design de PCB, abrindo novas possibilidades para interligações de alta densidade e aplicações avançadas. Ao compreender os tipos, os processos de fabricação e as considerações de design associadas às microvias, os designers de PCB podem aproveitar seu poder para criar dispositivos eletrônicos de ponta para o futuro.
Inscreva-se para participar do próximo webinar do ICAPE sobre a tecnologia HDI, onde compartilharemos mais conhecimentos e dicas para otimizar seus projetos e construções.