Leitfaden für Leiterplatten-Basismaterialien - Arten, Anwendungen , Vor- und Nachteile
Das Verständnis der in der Leiterplatten-Herstellung verwendeten Basismaterialien ist entscheidend für die Optimierung von Leistung, Zuverlässigkeit und Kosteneffizienz. In diesem umfassenden Leitfaden befassen wir uns mit den verschiedenen Rohmaterialien, die bei der Herstellung von Leiterplatten verwendet werden können. Wir beantworten Ihre wichtigsten Fragen und geben Ihnen wertvolle Erkenntnisse zum individuellen Einsatz.
Was sind Leiterplatten-Basismaterialien?
Leiterplatten-Basismaterialien bestehen aus organischen und nicht-organischen Substraten und der/den leitenden Schicht(en) aus Kupfer.
Organische Substrate bestehen aus Papierkernen, die mit Phenolharzen imprägniert sind, oder Schichten aus gewebten oder nicht gewebten Glasgeweben, die mit Epoxid-, Polyimid-, Cyanatester- oder BT-Harzen durchtränkt sind.
Zu den nicht-organischen Substraten gehören Keramik, Aluminium und Kupfer-Invar-Kupfer.
Die Wahl des organischen Materials hängt von den physikalischen Eigenschaften ab, die die Leiterplattenanwendung erfordert, wie z. B. Betriebstemperatur, Frequenz oder mechanische Festigkeit. Die Verwendung von nicht-organischen Materialien wird hauptsächlich durch die Notwendigkeit einer effizienten Wärmeableitung bestimmt.
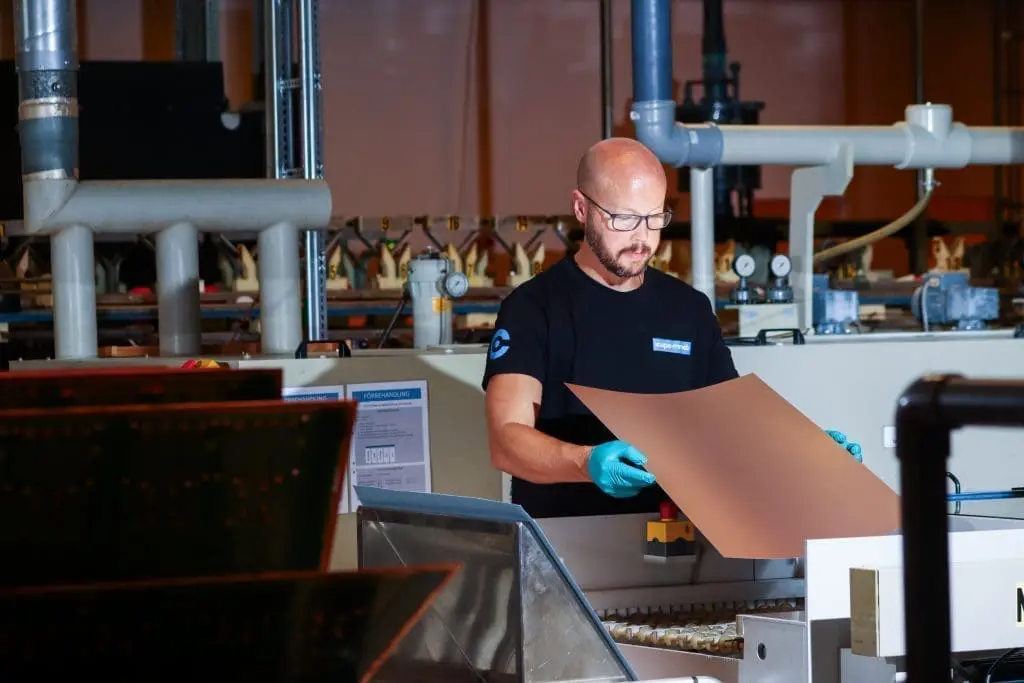
Arten von Leiterplatten-Basismaterialien
Substrate:
Substrate bilden die Basis, auf die das Kupfer aufgebracht wird. Diese Struktur dient als Träger für die Komponenten. Zu den gängigen Substratmaterialien gehören FR-4, CEM-1, CEM-3, keramikgefüllter Kohlenwasserstoff, PTFE, modifizierte Epoxidharze, BT (Bismaleimidtriazin), Aluminium, Keramik und flexible Materialien.
Leitfähige Materialien
Leitende Materialien werden für die Leiterbahnen, Pads und Durchkontaktierungen auf der Leiterplatte verwendet. Kupfer ist aufgrund seiner hervorragenden elektrischen Leitfähigkeit und seines günstigen Preises das am häufigsten verwendete leitfähige Material. Andere leitfähige Materialien sind Silber und Gold für Keramik-Leiterplatten.

Anwendungsspezifische Basismaterialien
Hochfrequenz-Anwendungen:
Für Hochfrequenzanwendungen bieten spezielle Materialien, wie modifizierte Epoxidharze oder keramisch gefüllte Kohlenwasserstoffe eine hervorragende elektrische Leistung, einen geringen dielektrischen Verlust und thermische Stabilität.
HF/Mikrowellen-Anwendungen:
Für HF/Mikrowellen-Anwendungen können keramisch gefüllte Kohlenwasserstoffe und keramisch gefüllte PTFEs die erforderlichen Leistungsanforderungen erfüllen.
Wärmemanagement:
Bei Anwendungen, die eine effiziente Wärmeableitung erfordern, werden IMS-Substrate (isolierte Metallsubstrate) wie Substrate auf Aluminiumbasis aufgrund ihrer hervorragenden Wärmeleitfähigkeit bevorzugt. Keramische Leiterplatten werden auch für Hochtemperaturanwendungen verwendet, bei denen das Wärmemanagement entscheidend ist.
Flexibilität und Platzbeschränkungen:
Flexibles Leiterplattenmaterial, wie z. B. Polyimid, ist ideal für Anwendungen, die Flexibilität erfordern und bei denen Platzmangel eine große Rolle spielt, wie z. B. bei tragbaren Geräten und medizinischen Implantaten (Herzschrittmacher, Hörgeräte u.ä.).
Anwendungen, Vorteile und Nachteile:
Leiterplatten (PCBs) sind integrale Bestandteile elektronischer Geräte und bieten mechanischen Halt und elektrische Verbindungen für verschiedene elektronische Komponenten. Die Wahl des Leiterplattenmaterials hängt von Faktoren wie den Anwendungsanforderungen, Kostenerwägungen und Leistungsspezifikationen ab. Im Folgenden finden Sie einige gängige Leiterplattenmaterialien mit ihren Anwendungen, sowie ihren Vor- und Nachteilen:
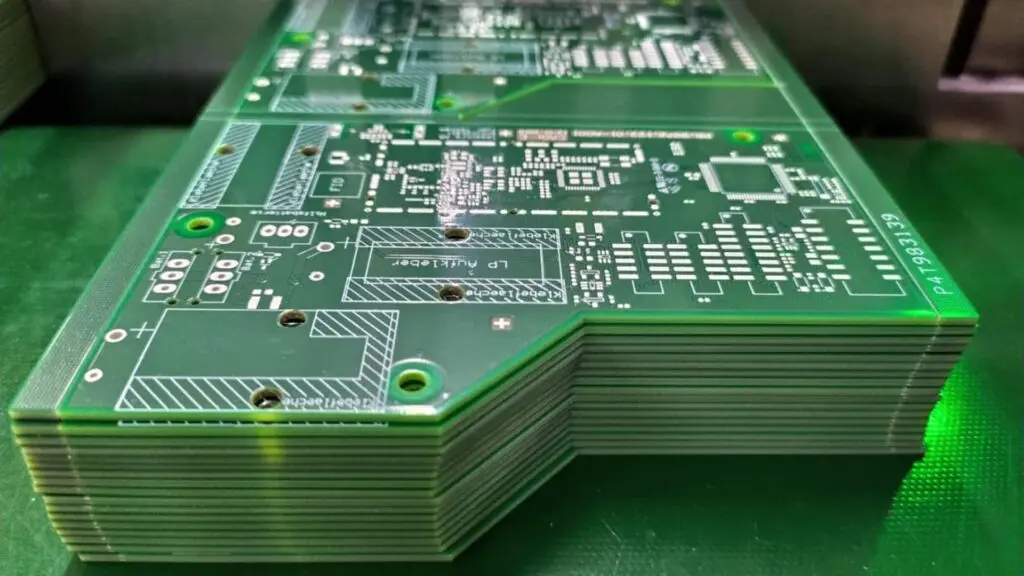
FR-4:
Anwendung: FR-4 ist das am weitesten verbreitete Leiterplatten-Basismaterial und eignet sich für eine Vielzahl von Anwendungen. Einsatzgebiete finden sich in der Unterhaltungselektronik, der Automobilelektronik, bei industriellen Steuerungen, sowie bei Anwendungen in den Bereichen Militär, Luftfahrt, Bahn- und Medizintechnik und mehr.
Vorteile:
Ausgezeichnete elektrische Isolationseigenschaften
Gute mechanische Festigkeit und Formbeständigkeit
Erschwingliche Kosten
Weithin verfügbar
Nachteile:
Begrenzte Wärmeleitfähigkeit
Nicht zum Stanzen geeignet
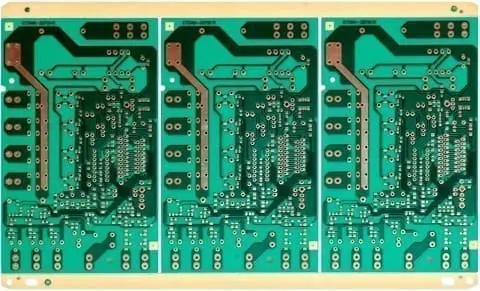
CEM-1:
Anwendung: CEM-1 wird häufig in preiswerter Unterhaltungselektronik und Haushaltsgeräten verwendet.
Vorteile:
Niedrige Kosten
Gute Stanzeigenschaften
Nachteile:
Nicht geeignet für doppelseitige Leiterplatten mit beschichteten Löchern
CEM-3:
Anwendung: CEM-3 wird üblicherweise in der Unterhaltungselektronik und in Haushaltsgeräten verwendet.
CEM-3 kann als kostengünstige Alternative zu FR4 verwendet werden, wenn keine höheren Anforderungen an die Leistungsfähigkeit gestellt werden.
Vorteile:
CEM-3 kann als kostengünstige Alternative zu FR4 verwendet werden, wenn keine höheren Anforderungen an die Leistungsfähigkeit gestellt werden.
Hat gegenüber CEM-1 den Vorteil, dass die Löcher durchkontaktiert werden können
Geeignet zum Stanzen
Nachteile:
Nicht so häufig verfügbar wie FR4
FR-4 mit modifizierten Epoxidharz-Systemen:
Anwendung: Diese Materialien werden häufig in Hochleistungsanwendungen wie HDI-Designs (High Density Interconnect), Luft- und Raumfahrt und Telekommunikation eingesetzt.
Vorteile:
Gute elektrische Leistung bei höheren Frequenzen
Geringere dielektrische Verlustwerte im Vergleich zu herkömmlichem FR4
Bessere thermische Stabilität als FR4
Nachteile:
Höhere Kosten im Vergleich zu Standard FR-4
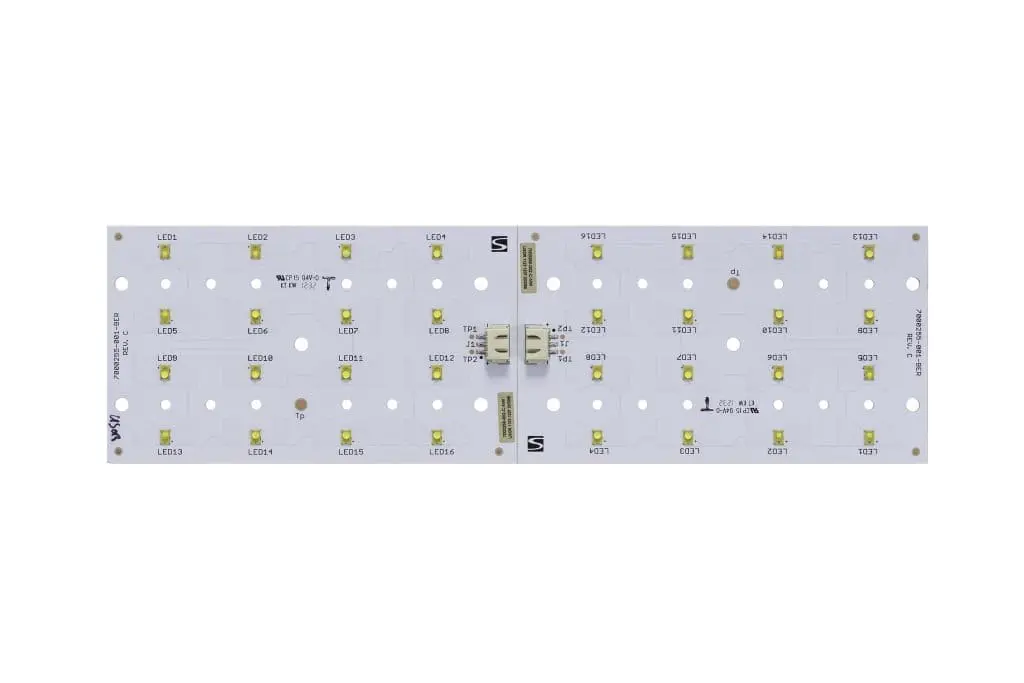
IMS-Leiterplatten:
Anwendung: IMS-Leiterplatten (isoliertes Metallsubstrat) werden wie Leiterplatten auf Aluminiumbasis in Anwendungen eingesetzt, die eine effiziente Wärmeableitung erfordern, z. B. LED-Beleuchtung, Netzteile und Automobilelektronik.
Vorteile:
Ausgezeichnete Wärmeleitfähigkeit
Leichtgewicht
Gute Formbeständigkeit
Relativ niedriger Preis
Nachteile:
Schwierig zu bearbeiten
Kompliziert bei der Herstellung von mehr als einer Schicht
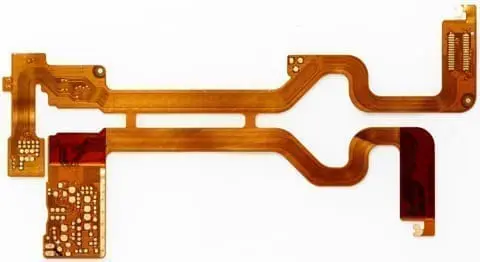
Flexible Leiterplatten (Flex-Leiterplatten):
Anwendung: Flexible Leiterplatten werden bei Anwendungen eingesetzt, die Flexibilität erfordern oder bei denen der Platzbedarf sehr groß ist, wie z. B. bei tragbaren Geräten, medizinischen Geräten und Automobilelektronik.
Vorteile:
Flexibilität und Biegsamkeit
Geringere Größe und Gewicht
Flex in Kombination mit starren Leiterplatten schafft zuverlässigere Leiterplattenverbindungen im Vergleich zur Verkabelung starrer Leiterplatten
Nachteile:
Höhere Kosten im Vergleich zu starren Leiterplatten
Begrenzte mechanische Festigkeit im Vergleich zu starren Leiterplatten
Keramische Basismaterialien:
Anwendung: Leiterplatten mit keramischen Basismaterialien werden in Hochtemperatur- und Hochleistungsanwendungen wie Leistungselektronik, LED-Gehäusen und Sensoren eingesetzt.
Vorteile:
Ausgezeichnete Wärmeleitfähigkeit
Hohe Temperaturbeständigkeit
Ausgezeichnete Dimensionsstabilität
Nachteile:
Höhere Kosten im Vergleich zu Standard FR-4
Die spröde Beschaffenheit kann eine vorsichtige Handhabung während der Montage erfordern
Nur sehr wenige Hersteller sind in der Lage, keramische mehrschichtige Materialien aufgrund des Herstellungsprozesses und der extremen Temperaturanforderungen herzustellen.
Schwierig zu bearbeiten
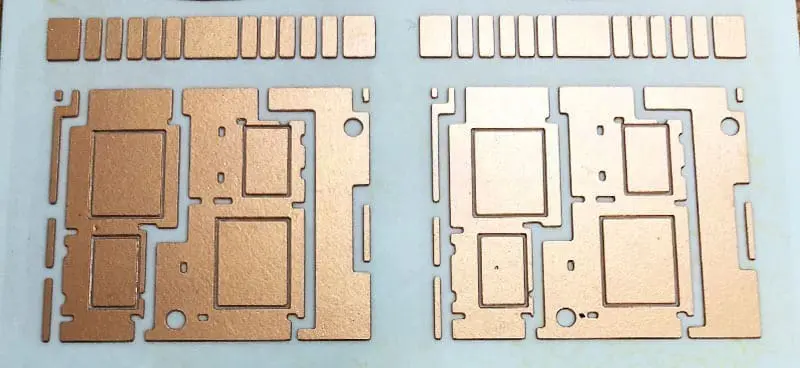
Keramisch gefüllte Kohlenwasserstoffe/PTFEs:
Anwendung: Diese Materialien werden häufig in Hochfrequenz- und Hochleistungsanwendungen wie HF/Mikrowellen-Schaltungen, Luft- und Raumfahrt und Telekommunikation eingesetzt.
Vorteile:
Ausgezeichnete elektrische Leistung bei hohen Frequenzen
Geringer dielektrischer Verlust
Gute thermische Stabilität
Nachteile:
Höhere Kosten im Vergleich zu Standard FR-4
Begrenzte Verfügbarkeit von spezifischen Formulierungen
Schlussfolgerung:
Das Verständnis der verschiedenen in der Leiterplatten-Fertigung verwendeten Rohmaterialien ist für die Optimierung der Leistung, Zuverlässigkeit und Kosteneffizienz elektronischer Geräte von entscheidender Bedeutung. Durch die Auswahl der richtigen Materialien auf der Grundlage anwendungsspezifischer Anforderungen kann der Kunde die optimale Leistung der Leiterplatte in ihrer Arbeitsumgebung erwarten.
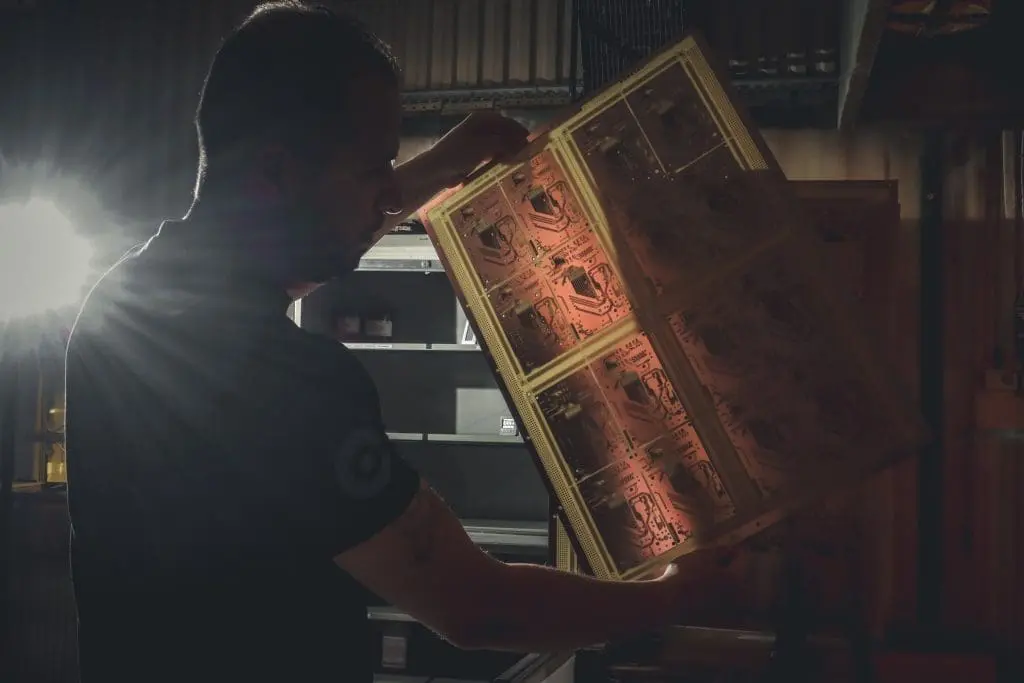
Häufig gestellte Fragen (FAQs) zu Leiterplatten-Basismaterialien:
Was sind Leiterplatten-Basismaterialien?
Leiterplatten-Basismaterialien, zu denen das Substrat und das leitende Material gehören, sind die grundlegenden Komponenten, die bei der Herstellung von Leiterplatten verwendet werden.
Welche Arten von Substraten werden in der Leiterplatten-Fertigung üblicherweise verwendet?
Zu den gängigen Substratmaterialien gehören FR-4, CEM-1, CEM-3, keramikgefüllte Kohlenwasserstoffe, PTFE, modifizierte Epoxide, Aluminium, Keramik und flexible Materialien. Jedes Substrat hat einzigartige Eigenschaften, die für verschiedene Anwendungen geeignet sind.
Welche leitfähigen Materialien werden für das Leiterbild auf Leiterplatten verwendet?
Kupfer ist aufgrund seiner hervorragenden elektrischen Leitfähigkeit und seines günstigen Preises das am häufigsten verwendete leitfähige Material. Weitere Optionen sind Silber und Gold, die für bestimmte Anwendungsfälle (keramische Leiterplatten, Steckerleisten, SMT-Oberflächen u.a.) eingesetzt werden.
Welche Vorteile bietet die Verwendung von keramisch gefüllten Kohlenwasserstoffen oder keramisch gefüllten PTFE-Materialien bei der Leiterplatten-Fertigung?
Diese Materialien bieten alle eine hervorragende elektrische Leistung, einen geringen dielektrischen Verlust und thermische Stabilität, was sie ideal für Mikrowellen- und Millimeterwellenfrequenzen und HF-Anwendungen macht.
Warum werden Leiterplatten auf Aluminiumbasis für das Wärmemanagement bevorzugt?
Leiterplatten auf Aluminiumbasis bieten eine hervorragende Wärmeleitfähigkeit und eignen sich daher für Anwendungen, die eine effiziente Wärmeableitung erfordern, wie z. B. LED-Beleuchtung und Leistungselektronik.
Was sind die Vorteile flexibler Leiterplattenmaterialien und in welchen Anwendungen werden sie üblicherweise eingesetzt?
Flexible Leiterplattenmaterialien, wie z. B. Polyimid, bieten Flexibilität, geringere Größe und geringeres Gewicht, was sie ideal für tragbare Geräte, medizinische Implantate und Automobilelektronik macht.
Wie unterscheiden sich keramische Leiterplatten von anderen Trägermaterialien, und was sind ihre Vorteile?
Keramische Leiterplatten bieten eine hervorragende Wärmeleitfähigkeit, Hochtemperaturbeständigkeit und Dimensionsstabilität, wodurch sie sich für Hochtemperatur- und Hochleistungsanwendungen wie Leistungselektronik und LED-Gehäuse eignen.
Was sind die wichtigsten Überlegungen bei der Auswahl von Leiterplatten-Rohmaterialien für eine bestimmte Anwendung?
Zu den zu berücksichtigenden Faktoren gehören elektrische Leistung, Anforderungen an das Wärmemanagement, mechanische Festigkeit, Kostenüberlegungen und Umweltfaktoren.
Wie kann ich die Qualität und Zuverlässigkeit von Leiterplatten-Rohmaterialien sicherstellen?
Qualitätssicherungsmaßnahmen, wie Materialtests, Lieferantenqualifikationen und die Einhaltung von Industriestandards (z. B., IPC-Normen), sind unerlässlich, um die Qualität und Zuverlässigkeit von Leiterplatten-Rohstoffen zu gewährleisten.